HMI vs SCADA – Breaking Down the Pros and Cons
If you are an operator, system integrator or control system engineer, choose HMI for direct interaction with machines and data visualization. However, for a more centralized and automated control over complex industrial processes, SCADA is the better option.
Key Differences Between HMI and SCADA
- Control Level: HMI is used for direct interaction with machines; SCADA is used for automated, supervisory level control over industrial processes.
- Data Visualization: HMI provides visual data readouts and interacts with devices at the operator level; SCADA collates, processes, and presents data at a systems overview level.
- Modern Uses: HMI has found wide use in high-performance touch screens and mobile remote monitoring; SCADA is moving towards incorporating technologies such as edge computing, AI, and machine learning.
- Cybersecurity: With the advancement to more connected and integrated systems, SCADA has raised cybersecurity concerns.
Comparison | HMI | SCADA |
---|---|---|
Interface | User interface/dashboard interacting with machine/system | Centralized monitor/control at supervisory level |
Implementation | Extend to various industries; monitor/input/output data; interface with PLCs & sensors | Automate complex industrial processes, fault detection, trend measurement, used across multiple industries |
Development | Touch screens, mobile devices, high-performance HMIs, Edge-of-network HMIs | Monolithic to distributed & networked systems; modern SCADA uses SQL databases, RAD capabilities |
Influences & Evolution | Influence of smartphones, Internet, & other modern technologies, adoption of AR/VR | 5G networks, Quantum computing, Edge computing, AI, Machine learning |
Data Interfacing | Data sent to cloud for remote access, mobile HMIs for remote data access | Collect live values from environmental conditions, record events into a log file |
Data Collection | RTUs, PLCs, other control devices, with SCADA systems | Discrete and analog sensors, field devices like RTUs or PLCs |
Benefits | Faster development, improvement in alarm resolution, less time spent navigating, faster identification of critical data | Automation, efficient and secure monitoring, cost-effectiveness, logging |
What Is HMI and Who’s It For?
HMI (Human-Machine Interface) is a dynamic interface connecting humans to machines, widely utilized in industrial environments. From displaying data and tracking production trends to overseeing KPIs, HMI is an invaluable tool for businesses striving for efficiency. With applications extending to various sectors like energy, manufacturing, power, and transportation, HMIs underpin the digital transformation of industries.
Primarily, HMIs are designed for operators, engineers, particularly control system engineers, and system integrators. Their widespread use can be attributed to their ability to interface with Programmable Logic Controllers (PLCs) and input/output sensors.
Pros of HMI
- Amplifies visualization of industrial processes
- Offers data centralization and digitization
- Enables remote monitoring and instant data access
- Adapts to modern mobile devices
Cons of HMI
- Dependent on GUI quality
- Level of sophistication varies based on implementation
What Is SCADA and Who’s It For?
SCADA (Supervisory Control and Data Acquisition) is a centralized monitoring and controlling application for complex industrial processes. This system is key to the smooth running of sectors like industrial plants, water and waste management, energy, and transportation, among others. SCADA systems detect, correct and measure trends over time, automating industrial operations.
SCADA’s reach extends to areas where efficient supervisory control and data acquisition are needed. From energy to waste and water management, its versatility allows it to be universally adopted. Essential roles interacting with SCADAs often include operators, engineers, and system supervisors.
Pros of SCADA
- Automates and controls complex industrial processes
- Efficient monitoring and secure data processing
- Compatible with a host of industrial sectors
- Expands to include technologies like artificial intelligence and machine learning
Cons of SCADA
- Higher initial cost
- Potential cybersecurity risks
Verdict: HMI or SCADA?
In the grand battle of HMI against SCADA, our verdict sways based on your job requirements. Here’s how we divide and conquer:
For System Integrators and Control Engineers
If your work involves intricate system integration or control engineering, HMI will serve as your better companion. Its proficiency in monitoring machine inputs and outputs, overseeing KPIs, and tracking production time makes it a compelling choice. It also affords extensive opportunities to incorporate AR/VR technologies, edge-of-network HMIs, and push data from local HMIs to the cloud for remote access and analysis.
For Operators in varying Industries
However, if you’re an operator in industries like energy, food and beverage, manufacturing, oil and gas, power, or recycling, both HMI and SCADA can be equally potent tools. Both systems accommodate extensive functionality, from monitoring temperature and operational status to controlling and visualizing all aspects of operations. SCADA systems also possess the flexibility to work with data historian software for long-term data analyses and trend spotting.
For Future-Shapers in Tech
If you’re frolicking in the tech future of 5G, edge computing, artificial intelligence, and machine learning, SCADA promises a comfortable playground. With evolution steering SCADA towards SQL databases, rapid application development capabilities, and inherent abilities to manage networked system supervisions, it’s poised to feed your high-tech hunger.
In summary, choosing between HMI or SCADA is a matter of application requirements. If you need a user-friendly interface with intricate monitoring capabilities, HMI excels. On the other hand, SCADA’s superior handling of complex industrial automation and future tech adoption makes it the optimal choice for extensive control networks.
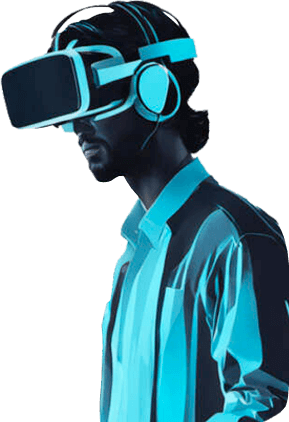