Top 11 Picks for ICS Alternatives in 2024
ICS encompasses a range of industrial control devices, systems, and networks crucial for automating industrial processes. It consists of elements like PLCs, RTUs, SCADA Servers, and more, used in sectors like manufacturing, transportation, and energy.
For those exploring substitutes to ICS, choices include SCADA, DCS, PLC, MES, IoT, BAS, DAS, RTU, ERP, MQTT, OPC.
SCADA
Stepping into the world of Control Systems, we meet SCADA, an acronym for Supervisory Control And Data Acquisition. This computer application truly stands as an emblem of supervisory prowess, monitoring and controlling plant or equipment at a centralized level and automating complex industrial processes.
SCADA Top Features
- Centralized Monitor: Provides an overwatch of a complete network.
- Automation of Complex Industrial Processes: Automates to detect and correct problems and measure trends over time.
- Components: A fusion of Remote Terminal Unit (RTU), sensors, control relays, SCADA master units, communication channels.
- Dual Nature Sensors: SCADA system incorporates discrete sensors to collect digital information from equipment, analog sensors to collect live values from environmental conditions.
- Human-Machine Interface: Serves as a master station, processes data and communicates data to human operator.
- Migration Support: The NetGuardian 832A supports a gradual migration over time to IP capable devices at remote sites.
Feature | Description |
---|---|
Modernization | Incorporates SQL databases, enables rapid application development (RAD), and eyes a future with 5G networks and quantum computing. |
Future Direction | Bears the promise of embracing edge computing, artificial intelligence, and machine learning. |
Scalability and Interoperability | Modern SCADA systems are scalable, interoperable, and improve accessibility to data and controls. |
SCADA Disadvantages
- Cost Factor: Utilizing PLCs often result in a long-run cost.
- Cybersecurity Concerns: Increased connectivity and system integration intensifies cybersecurity vulnerabilities.
- Legacy System: Legacy SCADA systems lack features like scalability, interoperability and have limited options for support.
SCADA Use Cases
Use case 1: Industrial Plants
SCADA proves itself a workhorse for industrial plants, streamlining complex processes, measuring trends and mitigating problems through its automation abilities.
Use case 2: Energy Sector
The energy sector can utilize SCADA for effective control of power plants, detecting issues in real time, and log event recording.
Use case 3: Transportation
SCADA’s network monitoring and control capacity wield significant benefits for the transportation sector, improving efficiency and safety of operations.
DCS
Introducing DCS, an acronym for Distributed Control System, where automation thrives in the midst of decentralization.
DCS: The Hallmarks of Innovation
- DCS enables individual control, affording process plants the luxury of bespoke reporting and monitoring components.
- Embrace DCS for its suite of configuration tools, tailored to facilitate database management, control logic, graphics, and security.
- DCS flawlessly supports modifications, upgrades, and seamless integration with your existing industry architecture.
- Witness DCS as it acts as centralized operator supervisory control—enhancing reliability, shaving off installation costs.
- Experience structure resilience with DCS, where single processor failure effects are significantly mitigated.
- Explore synchronicity with DCS under a common command structure, ensuring swift and proper information distribution.
- Marvel at the structural design of DCS, spanning workstations, stations, control units, communication systems, and smart devices alike.
Brand | Applicable Industry |
---|---|
Siemens | Power Generation |
ABB | Pharmaceuticals and Biotech |
Rockwell Automation | Oil and Gas |
Schneider Electric | Water Treatment |
DCS: The Other Side of the Coin
- When compared to PLC, DCS may not be the ideal controller for real-time actions.
- For smaller facilities with lesser I/O points, DCS may not be the best fit.
DCS Pricing
Specific pricing details vary among major DCS brands such as Siemens, Yokogawa, ABB, Honeywell, Rockwell Automation, Schneider Electric, & Emerson. Consult directly for the most accurate pricing information tailored to your requirements.
DCS Use Cases
Use case 1: Manufacturing
In manufacturing, DCS streamlines processes with controlled distribution, increasing safety and enhancing production efficiency.
Use case 2: Infrastructure
When implementing infrastructure projects, DCS supports easy maintenance throughout the plant life cycle.
Use case 3: Oil and Gas
The oil and gas industry benefits from DCS‘ robust control structures, leading to optimized interactions among numerous controllers.
OPC: Where Multivendor Integration Flourishes
In the interconnected space of industrial automation, Open Platform Communications (OPC) has risen as a standout telecommunication standard since its inception in 1996. Originally tagged as Object Linking and Embedding for Process Control (OLE), OPC was designed on the bedrock of facilitating real-time data communication between control devices from diverse manufacturers.
OPC: A Smorgasbord of Top Features
- Under-the-hood adherence to Microsoft’s OLE, COM, DCOM, and .NET Framework
- Comprehensive data interaction via OPC Data Access for real-time data reading and writing, and OPC Historical Data Access for archived data
- Synchronized handling of notifications using OPC Alarms and Events
- Rich scalability, flexibility, and security afforded by OPC Unified Architecture (UA)
- Seamless integration with XML and Web Services for MES and ERP support
Noteworthy Aspects | Details |
---|---|
OPC and Microsoft’s OLE | Facilitates real-time exchange of information between software applications and process control hardware |
OPC DA Protocol | Allows extraction of data from control systems, and transfer that information to other systems in a facility |
OPC UA | Offers end-to-end encryption, authentication, auditing – bolstering system security |
Downsides of OPC
- Some OPC specifications availability limited to OPC Foundation members
- Requires system integrators to receive mandatory training
- The necessary use of Microsoft’s OLE technology for certain applications
OPC Use Cases:
Use case 1: Interoperability
OPC is a boon for interoperability in the industrial automation space. Its communication standards allow for a seamless exchange of data between systems of multiple manufacturers.
Use Case 2: System Security
OPC UA provides a suite of security measures, including end-to-end encryption, authentication, and auditing. This makes OPC an ideal choice for industries prioritizing secure data interactions.
Use Case 3: Scalability and Flexibility
The OPC model views each device as an independent object. This approach ensures remarkable scalability and flexibility, accommodating needs across various sectors including software, hardware, M2M, and smart energy.
PLC
Conceived as a ‘Standard Machine Controller’ by General Motors in 1968, Programmable Logic Controllers (PLCs) revolutionized the manufacturing industry. These game-changing devices, originally designed to replace hardwired relays and timers, have continuously evolved since their inception, becoming smaller, faster, and more powerful.
PLC Best Features
- Increased functionality owing to advancements in processor and memory technology.
- Integration with ERP, MES systems, and SCADA, enhancing manufacturing operations’ efficiency.
- Standardized functions, inputs, and outputs, courtesy of the IEC 61131-3 Standard.
- Rapid development in Data Highway by Allen-Bradley and Modbus by Modicon, enabling PLCs to share information seamlessly.
- Adoption of advanced features such as vision system integration, motion control, and multiple communication protocols support.
Specialty | Details |
---|---|
Ladder Logic | This visual representation makes Boolean Logic easier to understand and use. |
Human-Machine Interface (HMI) | Developed in the 1990s, HMIs are now essential components in the industry. |
Monitoring and Recording | PLCs monitor and record run-time data, instrumental for start-stop processes and generating alarms during malfunctions. |
PLC Disadvantages
- Complexity can make troubleshooting difficult.
- Requires a highly skilled workforce to operate and maintain.
PLC Use Cases
Use case 1 – Factory Automation
PLC’s ability to monitor run-time data makes it indispensable in factory settings; it aids in achieving optimized efficiency and mitigating costly downtimes.
Use case 2 – Traffic Signal Control
PLCs significantly streamline the management of traffic signals, thanks to their ability to handle complex control systems.
Use case 3 – Advanced Production Equipment
PLCs seamlessly handle the control and monitoring of high-tech production equipment, such as robotic arms in cars and textile equipment, demonstrating their versatility.
MES
Meet MES, the game-changer in modern manufacturing. This computerized system transforms raw materials into finished goods, with an ability to control various elements, provide real-time information and drive production output. By bridging the gap between an Enterprise Resource Planning (ERP) system and a Supervisory Control and Data Acquisition (SCADA) system, MES serves as a backbone in manufacturing.
MES Top Features
- Product Lifecycle Management: Seamless tracking and management of a product’s life cycle.
- Resource Scheduling: Efficient resource allocation to improve productivity.
- Order Execution & Dispatch: Streamlined order processing for fast-paced production.
- Production Analysis: In-depth analysis for informed decision-making and strategy formation.
- Downtime Management: Effective management of downtime to minimise loss of production hours.
Feature | Benefit |
---|---|
Product Quality: | High emphasis on product quality for maximum customer satisfaction. |
Materials Tracking: | Real-time tracking of materials for smooth management. |
MES Downsides
- High Implementation Cost: The cost of implementing MES ranges from $375,000 – $1.2 million.
- Complexity: Custom-built MES solutions can be complex to integrate with existing IT systems and may require expertise for seamless functioning.
MES Pricing
MES doesn’t come cheap. But remember, quality comes at a price. The implementation cost of MES can range anywhere between $375,000 to $1.2 million.
MES Use Cases
Use Case 1: For Industries Seeking Regulatory Compliance
Utilize MES and keep auditor troubles at bay. Be it food, beverage or pharmaceuticals sector, MES offers as-built records, product tracking and improved quality control for perfect regulatory compliance.
Use Case 2: For Efficient Resource Management
MES is your ally when juggling with multiple resources. With efficient resource scheduling and real-time tracking of materials and equipment, make the best use of your resources without the fear of waste.
Use Case 3: For Data-Driven Decision Making
When major strategic decisions hang in the balance, MES comes to your rescue. With its powerful analytics and reports, make informed business decisions that are backed by data.
IoT
The Internet of Things (IoT) refers to a network of devices, powered with embedded sensors and software, that exchange data over the internet. A combination of low-cost sensors, connectivity, cloud computing, machine learning, and AI enables the practicality of IoT.
Top Features
- Operational efficiency: IoT enables efficient operations across sectors – from manufacturing to healthcare and agriculture.
- Business model creation: With the help of IoT, new business models and revenue streams can be generated.
- Asset Connectivity: IoT facilitates the connectivity and monitoring of assets, including automated farming equipment and remote machine considerations.
- Microcontroller-based: IoT devices use microcontrollers, which combine a microprocessor core, memory, and input/output ports to function.
Key Features | Benefits |
---|---|
Automated controls | Improved efficiency in processes via wireless automation |
Continuous monitoring | Regular updates on equipment health and performance |
Connected sensor data analysis | Analytics-driven forecasts and insights for improved decision making |
Limitations
- No inherent security mechanisms, exposing systems to potential vulnerabilities.
- Privacy concerns associated with the collection of sensitive data.
- Interoperability issues due to lack of standardization in IoT communication protocols.
Use Cases
Manufacturing
Within the manufacturing sector, IoT enables the measurement of production output, machine monitoring, and product quality check.
Fleet Management
Ideally suited for fleet management, IoT provides rerouting options based on variable conditions and boosts the efficiency and safety of the fleet.
Healthcare
In healthcare, IoT is adopted for remote patient monitoring and health analytics using wearable devices, enhancing patient care and experience.
BAS
The birth of Building Automation Systems (BAS) can be traced back to the 1600s, when Dutch innovator Cornelius Drebbel created the first HVAC controls system. Over years, with numerous technological advancements, including the evolution from pneumatic to direct digital controls in the mid-1980s and the development of interoperable protocols, contemporary BAS have drastically transformed the functioning of building services.
BAS Top Features
- Provides comprehensive control and integration of building services such as HVAC, lights, and security systems.
- Integrated with BACnet protocol, enabling interoperability.
- Supports green technologies, promoting energy, air, and water conservation.
- Use of modern controls frameworks like Niagara for protocol integration.
- State-of-the-art systems like ABB’S Aspect offer high efficiency and seamless integration with any BACnet device.
Feature | Benefit |
Scalable | Can grow with the building needs and integrate various systems. |
Energy-smart | Contributes to substantial energy savings and promotes sustainability. |
Multi-functional | Can manage heating, lighting, security, air quality, and more. |
BAS Limitations
- Improperly configured BAS account for significant energy use, approximately 20{66f7997927a862c9f57ec7dffc6a2fe6d405caee7001dff533b976d48fe118b1} of building energy use in the United States.
- Many traditional buildings’ systems operate independently, challenging the full integration of services.
BAS Use Cases
Use case 1
Modern green buildings, aimed at conservation, can largely benefit from BAS. With the ability to control energy consumption, air, and water quality, BAS proves to be a crucial part for green building structures.
Use case 2
Large commercial or industrial facilities with multiple systems may encounter difficulties coordinating each system’s operation. Here, an integrated BAS can provide a centralized management for these systems, enhancing efficiency and productivity.
Use case 3
Hospitals and healthcare centers, where safety is of utmost precedence, can rely on BAS to ensure a failsafe environment. From managing ventilation to access control, the services provided by a BAS contribute to a safer and more efficient patient care environment.
DAS
The DAS or Distributed Antenna System reinvents poor in-building coverage by implementing a network of small antennas, acting as repeaters, which are connected to a central controller tied to the wireless carrier network’s base station.
Top DAS Features
- Improved Coverage: DAS excels at enhancing indoor cellular network performance.
- Modular and Scalable: DAS can handle up to 240 analog or digital outputs and supports various input types.
- Flexible Installations: DAS deployments can be passive or active, influencing the signal distribution method and extent.
- Shared Solution: The cost of DAS system can be shared by multiple carriers to reduce expense.
- Effective Management: DAS management is simplified with AIMOS, ensuring optimized network performance and operational efficiency.
Pros | Cons |
---|---|
Improved signal coverage in densely populated indoor areas. | High costs due to labor-intensive installation processes. |
Modular, allowing interface with any experiment to computer for data recording/processing. | Costs may necessitate carrier involvement. |
DAS Downsides
- High Installation Costs: The complex nature of DAS installation requires significant labor, leading to high costs.
- Carrier Dependence: The costs of DAS deployment are often borne by the carrier. This necessity for carrier involvement may pose limitations.
DAS Pricing
Exact DAS pricing will depend on various factors including travel distance, building characteristics, existing infrastructure and technical demands. Only after comprehensive site surveys and RF benchmarking can accurate cost ranges be provided.
DAS Use Cases
Use Case 1: Large Indoor Spaces
In densely populated indoor spaces such as malls or high-rise buildings, DAS can enhance in-building cellular network performance.
Use Case 2: Network Management
With its robust management capabilities, DAS streamlines operations and maintenance in network management scenarios.
Use Case 3: Data Intensive Facilities
In data-intensive settings like medical centers, DAS can handle up to 240 analog or digital outputs efficiently.
RTU
An RTU (Remote Terminal Unit) is a sophisticated microprocessor-controlled electronic device designed to operate in both remote and harsh conditions. These highly resilient units function as an interface between real-world objects and distributed control or SCADA systems, transmitting essential telemetry data while also taking critical control messages from the master supervisory system.
RTU Top Features
- Highly operational in extreme environments and hard-to-reach locations.
- Possesses a specific design to handle harsh conditions.
- Transfers data to the SCADA Master Station, providing essential monitoring.
- Includes components such as a CPU, communication interfaces, and several other circuit cards for maximum efficiency.
- Supports the IEC 61131-3 programming standard, enhancing programming flexibility.
- Shares a communications line with multiple RTUs or IEDs in a multi-drop scheme.
Key Features | Benefits |
---|---|
Power efficiency | Helps sustain operations with limited power resources; can be solar powered |
Telemetry data sending | Enables remote tracking and monitoring |
Physical override switches | Allows for manual control during maintenance or emergency situations |
RTU Limitations
- Requires special setup software to connect data input streams to data output streams, defining communication protocols and troubleshooting installation issues.
- High-end models can be significantly more expensive due to advanced features.
RTU Pricing
RTUs come with varying price points depending on their capacities, functionalities, and brand reputation. Entry-level models begin at approximately $500, while premium models can exceed $5,000.
RTU Use Cases
Industry Use
Used extensively for remote monitoring in global industries such as oil and gas, electric, water utilities, refineries, food processing, automobile manufacturing, and others.
Extreme Environments
With durability at its core, RTUs are perfectly suited for monitoring in extreme environments like the Biosphere 2 project.
Grid guarding systems
RTUs play a crucial role in pipeline and grid guarding systems, offering high-level control and monitoring capabilities.
ERP
Enterprise Resource Planning (ERP) are catalysts for a seamless integration of business functions. ERP systems orchestrate all processes necessary to run a company, ensuring efficiency, accuracy, and maximizing productivity. Evolving from the Material Resource Planning (MRP) systems, ERPs have been at the heart of business technology for the past 60 years.
ERP Top Features
- ERP has transformed into a repository of key business information, providing accurate, real-time data for proactive decision making.
- With the advent of Cloud ERP, these systems have become more efficient and accessible, eliminating the need for dedicated hardware and trimming down IT staff requirements.
- ERP systems have embraced innovative technologies like Artificial Intelligence(AI), Internet of Things(IoT), opening new avenues of data harnessing and predictive analysis.
Year | Evolution Stages |
---|---|
1960s | Material Requirements Planning (MRP)systems, initial ERP model, first launched. Used primarily for inventory and production tracking. |
1980s | Manufacturing Resource Planning (MRP II) systems introduced with advanced scheduling capabilities. |
1990s | Introduction of Cloud ERP, making systems accessible to wider businesses. |
2000s | Internet-enabled ERPs (ERP II) allowing seamless remote access. |
ERP Limitations
- Unsuccessful implementation of ERP systems might result in inefficiency or ineffective operations.
- Despite cloud technology reducing costs, ERPs can still be expensive particularly for smaller business.
- ERP solutions, requiring ongoing maintenance and updates, could encounter unexpected operational hitches.
ERP Use Cases
Use case 1: Large Corporations
ERP is an indispensable tool in larger companies, providing a broad spectrum of applications ranging from inventory management to detailed reporting. ERP software enables such businesses to maintain smooth operations and make data-driven decisions.
Use case 2: Manufacturing Sector
From its roots in simpler MRP systems, ERP has always been a critical tool in production and manufacturing, offering enhanced scheduling capabilities and the power to make real-time adjustments to operations.
Use case 3: Smaller Businesses
Cloud-based ERP solutions, necessitating less hardware and IT investment, provide smaller businesses the ability to harness the power of ERP. These businesses can now get comprehensive insights and enhance business operations at a fraction of the traditional costs.
MQTT
MQTT, or Message Queuing Telemetry Transport, is an ISO/IEC PRF 20922 certified protocol, originally developed for low-bandwidth, high latency networks. Once primary to the oil and gas industry, today it sails through the powering tide of digital services, mobile capabilities, edge computing, lending a hand to Industrial Internet of Things (IIoT) and Internet of Things (IoT) applications.
MQTT Top Features
- Publish-subscribe architecture: This decouples data-producing devices from data-consuming applications, thus facilitating an efficient flow of information.
- MQTT supports a variety of languages including Python, streamlining its implementation.
- Enabled with modern authentication protocols (like OAuth, TLS1.3), it guarantees a secure data exchange environment.
- An additional specification, Sparkplug, heightens MQTT’s capabilities for mission-critical applications.
- The protocol can be wrapped in a WSS envelope for direct data reception into web browsers.
Compatibility | Description |
---|---|
Low-bandwidth networks | MQTT works with low-bandwidth networks, allowing efficient, secure exchange of data. |
Security Measures | Includes collaborations with firewalls, VPNs, IPsec to safeguard IoT systems from breaches and data compromises. |
Compliance | MQTT has been adopted as a standard by OASIS and ISO/IEC ensuring its lawful application in varied spheres. |
MQTT Limitations
- As MQTT builds upon TCP/IP, environments lacking this framework may face constraints implementing the protocol.
- MQTT’s scalability, although advantageous in most scenarios, may present challenges in maintaining quality of service when dealing with significant loads.
MQTT Use Cases
Interacting with AWS IoT Core
MQTT finds substantial use in connecting billions of IoT devices and routing trillions of messages to AWS services, integrating smartly into scalable and secure tech ecosystems.
Remote Data Collection
In industries like hydraulic fracturing operations, remote data collection is a storefront task. MQTT enhances the efficiency and security of this data integration, boosting industrial automation capabilities.
Smart City Designs
MQTT Protocol has found applications in smart city PoC designs for message transport, reinforcing the role of tech in shaping greener and smarter cities.
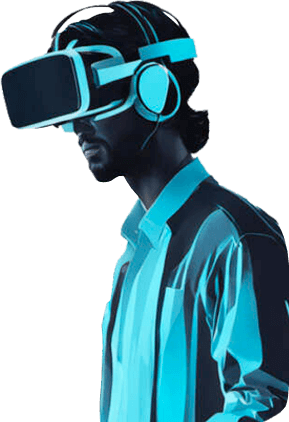