Explore 5 Top IIoT Alternatives for 2024
IIoT or Industrial Internet of Things is a smart sensor-based system revolutionizing industrial processes through data collection, exchange, and analysis for enhanced efficiency across sectors like manufacturing, energy management, utilities, and oil & gas. It enables predictive maintenance, improved field service, energy management, and asset tracking. The IIoT market is projected to grow significantly, reaching $516.6 billion by 2028.
For those exploring alternatives to IIoT, choices include RPA, PLC, DCS, Microcontroller, Relay.
RPA
Your search for an alternative ends here with Robotic Process Automation (RPA). It gives power to your business by automating workflows and eliminating mundane tasks with minimal upfront investment. More than that, it’s scalable, enterprise-ready, and emulates human actions interacting with digital systems.
RPA Top Features
- Deployment of software robots emulating human’s actions interacting with digital systems.
- Able to work with semi-structured or unstructured data, visualizing screens including virtual desktops.
- Application in legacy systems lacking APIs, virtual desktop infrastructures (VDIs), or database access.
- Integration capabilities with AI and machine learning.
- Increased employee satisfaction and productivity due to automation of routine tasks.
Features | Benefits |
---|---|
Integration with AI | Enables RPA to handle cognitive processes requiring complex decisions |
RPA and process mining | Results in intelligent process automation |
Undisruptive to underlying systems | Scalable and enterprise-ready |
RPA Disadvantages
- Limited to processes that are rule-based and repeatable
- Dependent on application interfaces — significant changes can affect their functioning
- Certain level of technical knowledge required for implementation and maintenance
RPA Pricing
RPA’s pricing starts at $5,000 and can reach $15,000 but costs can elevate to millions for company-wide automation. Costs are influenced by factors such as vendor pricing, number and complexity of bots in deployment, initial process analysis, engineering costs, and third-party RPA integrations.
RPA Use Cases
Use case 1: Finance
RPA is highly beneficial in financial sectors owing to its proficiency in performing rule-based, high volume tasks, thus increasing operational efficiency, compliance, and customer service.
Use case 2: IT Operations
In the realm of IT, RPA paves the way for cost reduction, optimization of processes and improved customer experiences.
Use case 3: Legacy Systems
When dealing with legacy systems that lack APIs, VDIs, or database access, RPA offers seamless integration and automation.
PLC
The first invention that led to a revolution in controlling manufacturing processes, Programmable Logic Controllers (PLC), was conceptualized and developed by General Motors in 1968. PLCs are the resilient systems that, for decades, have automated complex processes while continuously emerging with enhanced features due to advancements in technology.
PLC Top Features
- Speed: Brought on by the inexpensive microprocessor revolution in the 70s, PLCs have constantly evolved to work at faster rates.
- Standardization: The introduction of IEC 61131-3 Standard brought consistency, standardization of commands, inputs, outputs, and increased ease of understanding for programmers.
- Data Handling : PLCs have continually been the frontrunners in managing big data and artificial intelligence on the factory floor, thanks to major advancements in memory and processing technology.
- Ease of Integration: Today’s PLCs seamlessly integrate with ERP, MES systems, and SCADA, significantly boosting manufacturing operations’ efficiency and performance.
Year | Milestone |
1960s | Invention of the first PLCs, replacing hardwired relays and timers. |
1980s | Introduction of third-party software packages, bringing down the cost of programming devices. |
1990s | The integration of PLC software with Human-Machine Interface (HMI). |
PLC Downsides
- PLCs can be intricate to troubleshoot.
- PLCs require a skilled workforce for efficient operation and maintenance.
PLC Use Cases
Use case 1
PLCs find extensive use in automating car assembly lines, efficiently operating robotic arms that assemble cars rapidly and without errors.
Use case 2
In the aviation industry, PLCs have taken critical hold, controlling airport runway systems.
Use case 3
Industrial applications such as control of air compressors, also heavily rely on the precision and efficiency of PLCs.
DCS
Open your eyes to the marvel of management, the titan of tech, the supreme sovereign of smart…meet DCS (Distributed Control System). This automated control system is no mere distribution system, it’s revolutionizing industries by managing and controlling processes like you’ve never seen before!
DCS Top Features
- Decentralized Control Principle: Allows individual control, ensuring smooth operation across the board.
- Set Configuration Tools: Provides comprehensive database management, control logic, graphics, and system security. Talk about wearing multiple hats!
- Supports Upgrades: Easily integrates with existing industry architecture and supports modifications and upgrades. Who doesn’t love growth and adaptability?
- Centralized Operator Supervisory Control: Enhances the reliability of operations and slashes installation costs down to a minimum.
Feature | Benefit |
---|---|
Smart Devices | Translates to overall enhanced functionality and user experience. |
Robust Structure | Truly robust. Even a single processor failure doesn’t put your system out of action. |
DCS Downsides
- DCS is more suited to larger facilities dealing with massive I/O points.
- While PLC makes real-time actions its specialty, DCS requires more comprehensive processes and systems.
DCS Use Cases
Use case 1
DCS simply shines in the power generation sector, showcasing a strong design including engineering workstations, operating stations, process control units, and smart devices.
Use case 2
Revolutionizing the oil and gas industry where advanced control and large-scale facilities are the norm, DCS steps up, reducing downtime and pushing production efficiency through the roof.
Use case 3
The pharmaceutical and biotech industry embraces DCS wholeheartedly. Why? Such facilities benefit from the decentralized control principle and ease of plant life cycle maintenance that DCS provides.
Microcontroller
A microcontroller, also known as an embedded controller or a microcontroller unit (MCU), is a compact integrated circuit that governs a specific operation in an embedded system. It combines the functions of a microprocessor, memory, and peripherals on one chip, making it a cost-effective and power-efficient solution for various industries.
Microcontroller Top Features
- Integrated processor, memory, and I/O peripherals on one chip
- Variable memory types including volatile memory (RAM) and non-volatile memory (flash memory, EPROM, EEPROM)
- Sophisticated processor that can range from 4-bit, 8-bit, 16-bit to higher complexity processors
- Embedded with Analog to Digital Converter (ADC) and Digital to Analog Converter (DAC) for effective external device communication
- Based on advanced Harvard or von Neumann architecture for efficient data exchange
- Coding in multiple programming languages like C, Python, and JavaScript
- Can be programmed either using complex instruction set computing (CISC) or reduced instruction set computing (RISC)
Component | Description |
---|---|
System Bus | Helps in connecting different microcontroller components |
Serial Port | Allows connection with external components |
Ferroelectric RAM, NOR Flash, OTP ROM | Efficient resources for program memory |
Microcontroller Limitations
- Less sophisticated than System on Chips (SoCs)
- Performance-critical roles might require higher clock speeds, power consumption, and robust memory
- Choosing a microcontroller requires considering factors like maximum speed, amount of RAM or ROM, types of I/O pins on MCU, power consumption and constraints, development support, and availability in the market
Microcontroller Use Cases
Use case 1: Industrial Automation
In industrial automation, microcontrollers play a key role in managing the basic functions of larger components without any complex front-end operating system.
Use case 2: Robotics
Microcontrollers find valuable use in robotics, wherein they interpret data by the central processor, governing specific operations of the robot.
Use case 3: Automotive
The automotive industry uses microcontrollers extensively in vehicles to govern various operations under varied temperature and tough conditions.
Relay
Embarking on a journey with Relay, an electrically operated switch behemoth, which leverages independent low-power signal to dictate circuit(s). Originating from telegraph circuits and early computers, this traditional form resorts to an electromagnet to open/close contacts, with alternatives utilizing solid-state relays with semiconductors.
Relay Top Features
- Relay optimizes repetitive, time-driven, and high-speed control operations, conquering data acquisition and manipulation requirements.
- It becomes cost-effective when replacing 3-4 or more relays, triggering cost savings in equipment, installation, troubleshooting, and labor.
- Reprogrammable, offering flexibility in altering control schemes. Relay technology brings forward transferable programs and minimal debugging time.
- Advanced Functions: Perform wide variety of control tasks, ranging from single repetitive action to complex data manipulation.
Flexibility | System updates and modifications swiftly carried out via keystrokes |
Communications | Facilitates data collection and information exchange with operator interfaces, other PLCs, computers. |
Speed | Quick response capability apt for automated machines |
Diagnostics | Built-in troubleshooting capability with programming devices allowing quick resolutions. |
Relay Limitations
Compatibility | While largely compatible, might struggle with certain niche industrial/automation systems. |
Learning Curve | Though Relay provides a comprehensive electrical skills education system, beginners may find it a touch complex. |
Relay Pricing
Due to constraints of the provided company summary, specific pricing details of Relay have been omitted from this blog post.
Relay Use Cases
Use case 1: Packaging Operations
Relay is tailor-made for packaging operations, providing quick controls, enhanced communications and time-driven functions.
Use case 2: Machine Controls
For various machine controls, Relay’s superior data manipulation capabilities make it a reliable companion.
Use case 3: Traffic Light Sequencing
In traffic light sequencing, Relay’s event-driven operations and high-speed control make it ideal.
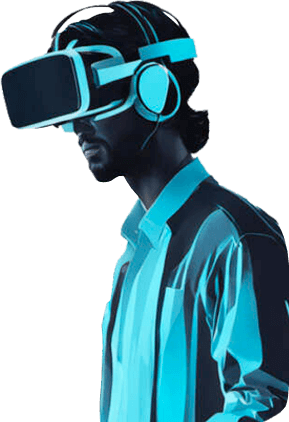