Which Reigns Supreme: PLC or DCS?
Key Differences Between PLC and DCS
- Scope: PLC suits real-time, compact applications; DCS is designed for larger facility management and complex process control.
- Interactivity: DCS optimizes interactions between multiple controllers, perfect for larger I/O handling.
- Adaptation: PLCs have evolved with advancing technology, their functionalities now extending into ERP, MES, and SCADA systems. DCS maintains dominance in centralized process industries.
- Growth: PLCs and PACs are merging, introducing advanced tech to low-tier machines. DCS market is projected to reach $23.2 billion by 2026.
For real-time, compact applications, go with PLC. It’s deeply ingrained in modern manufacturing, thanks to its evolution alongside technology. DCS, ideal for larger, more advanced process controls, reigns supreme in centralized industries. Select according to scope, adaptability and future growth potential.
Comparison | PLC | DCS |
---|---|---|
Initial Development | 1960s | Varies by Brands listed |
First Developer | General Motors | Varies by Brands listed |
Impact on Operations | 60{66f7997927a862c9f57ec7dffc6a2fe6d405caee7001dff533b976d48fe118b1} reduction in machine downtime when first tested | Increases safety, enhance production efficiency |
Innovation | Use of ‘ladder logic’ against ‘Boolean Statements’ | Enables individual control, reporting, monitoring components in process plants |
Technological Progress | Constant evolution toward smaller, faster, more powerful systems | Network abilities pivotal in process management |
Software Standards | IEC 61131-3 Standard | Uses configuration tools for database management, control logic, graphics, system security |
Applications | Automating processes in industries like auto manufacturing, air compressors, airport runway control, traffic signal control, textile equipment etc. | Used in power generation, oil and gas industry, water treatment, pharmaceuticals and biotech, manufacturing, infrastructure |
Benefits | Flexibility, error correction, saves space, low cost, easy testing and troubleshooting | Centralized operator supervisory control, enhances reliability, reduces installation costs |
What Is PLCs and Who’s It For?
Programmable Logic Controllers (PLCs) reign supreme in the world of automation, a crucial cog in modern manufacturing operations. Born in the 1960s to supplant cumbersome hardwired relays and timers, PLCs have evolved to be smaller, quicker, and brimming with power. Today’s PLC prides itself on being an integrative solution, facilitated by advancements in processors and memory technology, marrying enterprise resource planning (ERP), manufacturing execution systems (MES), and Supervisory Control and Data Acquisition (SCADA).
Intended for industries leaning towards automation, PLCs find their niche among businesses seeking robustness and operational efficiency. From robotic arms in car assembly to traffic signal and smoke alarm control, PLCs drive operational excellence for a plethora of applications.
Pros of PLCs
- Maximal Flexibility
- Error Correction Capabilities
- Space-saving design
- Lower costs in the long run
- Easier testing and troubleshooting
Cons of PLCs
- Troubleshooting can be complex
- Demand for skilled workforce
What Is DCS and Who’s It For?
The Distributed Control System (DCS) revolutionizes process industries with its decentralized control principle. Billed to experience a surge in global revenues to $23.37B by 2025, DCS caters to the pivotal need for versatile processing management across diverse functionalities. Its ingenious design structure allows for maximal reliability while cutting down on installation costs.
DCS finds its application in industries spanning power generation, oil and gas, water treatment, pharmaceuticals, biotech, manufacturing, and infrastructure. With its robust architectural integration, easy upgrades, and centralized operator supervisory control, DCS caters to larger facilities dealing with substantial I/O points.
Pros of DCS
- Effective handling of substantial I/O points
- Increased safety and production efficiency
- Ease of maintenance throughout the plant life cycle
- Optimized interaction among numerous controllers
Cons of DCS
- Higher initial investment
- Requires large-scale integration
The Ultimate Showdown: PLC or DCS?
In the fierce battle of Programmable Logic Controllers (PLC) and Distributed Control Systems (DCS), unique purposes dictate the victory. Here’s our conclusive verdict.
Industrial Process Automation
PLC takes the trophy here. Developed for manufacturing automation, PLCs offer robust control, easy programming, and integration with SCADA and ERP systems. Perfect for sectors requiring quick, real-time decisions like the automotive or textile industry.
Large-Scale Enterprises
Opt for DCS. For larger facilities with thousands of I/O points, DCS offers advanced process control, enhances safety, increases efficiency, and eases maintenance. Top player in power generation, oil and gas, and pharmaceutical sectors.
New Age Innovators
Choose PLC. With reduced size and cost, incorporation of advanced tech, and data acquisition-tools; PLCs suited for innovators seeking practical, cost-effective solutions for smaller-scale projects or start-ups.
Emerging Process Industries
Turn to DCS. With an edge in innovative, emerging process industries, the decentralized control principle of DCS comes out on top. Ideal for making significant industry-wide changes.
If youcrave real-time actions, the simplistic but powerful PLC wins over. But for substantial I/O points in gigantic facilities needing advanced process control, DCS outshines. A clear-cut verdict doesn’t exist in the PLC vs DCS debate; it’s the purpose that commands the choice.
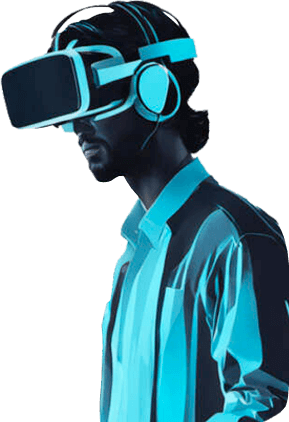