Who Should You Bet On: PLC or Relay?
For meticulous control operations and interfacing with advanced industrial systems, PLCs reign superior due to their programmability, integration abilities, and robust data tracking. However, if cost-effectiveness, simplicity, and rapid-response are top priorities, opt for Relays. It’s optimal for repetitive, time-driven tasks, and offers less complexity.
Key Differences Between PLC and Relay
- Coding: PLCs require advanced programming knowledge while Relays do not require coding.
- Function: PLCs offer intricate control over processes, Relays serve for straightforward on/off functions.
- Cost: PLCs generally come with higher upfront costs. Relays are more cost-effective, particularly when replacing a small number of existing relays.
- Integration: PLCs integrate better with MES systems, SCADAs, and other advanced tech while Relays offer limited integration capabilities.
- Data Management: PLCs can monitor, record and process large volumes of data. Relays aren’t equipped for complex data handling.
Comparison | PLC (Programmable Logic Controllers) | Relay Control System |
---|---|---|
Definition | A digitally operating electronic apparatus with a programmable memory | An electrically operated switch, controls circuits via independent low-power signal |
Development Epoch | 1960s | Used in early computers, long-distance telegraph circuits, telephone exchanges |
Advancements | Integrated with ERP, MES systems, SCADA, advanced capabilities due to processor, memory tech advancements | Alternate forms utilize solid-state relays with semiconductors |
Application Areas | Robotic arm in cars, air compressors, airport runway control, traffic signal control, smoke alarm control, textile equipment | Conveyors, form-fill operations, packaging, traffic light sequencing, gate control, various machine controls |
Benefits | Flexibility, low cost, easy testing and troubleshooting, corrects errors, saves space | Cost-effective, provides compact solution, reprogrammable, facilitating easy control scheme alterations, reduced programming time |
What Is PLCs (Programmable Logic Controllers) and Who’s It For?
PLCs is a technology conceived in the 1960s to automate processes, primarily in the manufacturing sector. The devices have greatly evolved since, from suitcase-sized units to compact, faster alternatives brimming with advanced capabilities, thanks to the progress in processor and memory technologies. HIP: PLCs are intended for use in industries seeking to advance the efficiency and performance of their operations, such as control systems manufacturing.
Pros of PLCs
- PLCs offer flexibility, correct errors, save space, and low cost.
- They make testing and troubleshooting easy.
- PLCs’ integration with ERP, MES systems, SCADA enhances manufacturing operations’ efficiency and performance.
Cons of PLCs
- PLCs troubleshooting can be difficult.
- The technology requires a skilled workforce for operation.
What Is Relay and Who’s It For?
Relay is an electrically operated switch that controls circuit(s) via independent low-power signals. Born from use in long-distance telegraph circuits, telephone exchanges, and early computers, its application today spans multiple industrial and automation systems. HIP: Relay is intended for control applications that require coordinated operation of electrical/electronic devices, including conveyor, packaging operations, traffic light sequencing, and gate control.
Pros of Relay
- Cost-effective when replacing 3-4 or more relays.
- Compact and reprogrammable for flexibility and easier control scheme alterations.
- Facilitates data collection, information exchange with interfaces, PLCs, and computers.
Cons of Relay
- Replacement can be cost-intensive for less than 3-4 units.
- Requires hardware for diagnostic and troubleshooting.
The Verdict Is In: PLC vs Relay – Choose Wisely
Evaluating the rivers of analysis and wisdom flowing through the digital discussion on PLCs and Relays, a clear conclusion surfaces for distinct audience segments.
Automation Engineers
PLCs shine as a beacon for quality control and system optimization. Backed by the adaptability of Ladder Logic and boon of HMIs, this superior technology promises speedy programming and comprehensive troubleshooting. With its flexibility and advanced capabilities, PLCs are evidently the unmatched choice for modern manufacturing automation.
Industrial Technologists
Driven by Relays’ cost-effectiveness, this technology is ideal for orchestrating repetitive, event-driven tasks. With just a few clicks, you can modify the program, facilitating swift updates in control schemes. For factories dealing with conveyors, packaging, and basic machine controls, Relays fit the bill.
Programming Enthusiasts
For those relishing equipment that speaks high tech but with ease, PLCs come to the fore. Visual grace, raw power, or simplicity – everything can happen at your fingertips with PLCs. Ladder Logic with its visual representation makes the coding process not just logical but intuitive.
Glancing at the PLC vs Relay debate, with its roots firmly planted in size, cost, speed, and flexibility, it’s clear – for complex, high-level automation designs, you’ll want the sophistication of a PLC. Yet, for affordable solutions and simple tasks, the cost-effective Relay shines.
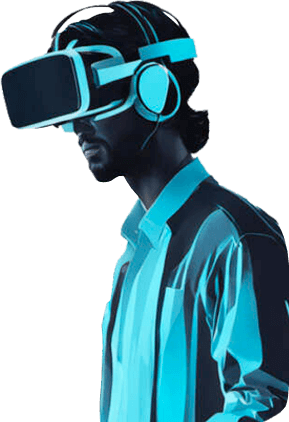