First Impressions: SCADA vs OPC
For users valuing easy access to field data from plant floor devices, OPC offers an effective solution with extra flexibility and comprehensive security measures. However, for complex industrial process automation and monitoring, the scalability and broad application range of SCADA makes it a more suitable option.
Key Differences Between SCADA and OPC
- Scope: SCADA focuses on supervisory level control and data acquisition. Meanwhile, OPC concentrates mainly on real-time data communication between devices.
- Application: SCADA is extensively used in various industries for automating complex processes. OPC predominantly ensures easy access to field data in plant floor devices.
- Security: Both SCADA and OPC address cybersecurity, yet OPC Unified Architecture provides added end-to-end encryption, authentication, and auditing.
- Future Direction: SCADA incorporates modern technologies such as 5G, quantum computing, artificial intelligence, and machine learning. OPC in contrast, focuses on supporting a wide range of platforms from embedded microcontrollers to cloud infrastructures.
Comparison | SCADA | OPC |
---|---|---|
Foundation | Supervisory Control and Data Acquisition | Industrial automation task force in 1996 |
Control Systems | Monitors and controls industrial processes | Data communication between control devices from different manufacturers |
Applications | Industries including oil, gas, water and waste control, telecom, energy, transportation | Building automation, discrete manufacturing, process control |
Components | RTU, sensors, control relays, SCADA master units, communication channels | Microsoft’s .NET Framework, XML, OPC Foundation’s binary-encoded TCP |
Future Directions | 5G networks, quantum computing, AI, machine learning | Wider range of platforms from embedded devices to cloud infrastructure |
Cybersecurity Concerns | More integrated and connected systems, risk of cyber attacks | OPC UA provides end-to-end encryption, authentication and auditing |
What Is SCADA and Who’s It For?
SCADA (Supervisory Control and Data Acquisition) is a centralized computer application designed to monitor and control a network of plants or equipment at supervisory levels. It excels in automating complex industrial processes, providing problem detection and correction, and measuring trends over time. SCADA is especially used in industries including water and waste control, energy, oil and gas refining, transportation, and telecommunications.
This system is instrumental for those looking to harness efficiency through automation and control of industrial processes, both locally and in remote locations. Whether you operate in energy, manufacturing, power, or transport, SCADA can be a game-changer.
Pros of SCADA
- Centralizes monitoring and control of complex industrial processes
- Capable of detecting and correcting issues while measuring trends
- Encompasses a wide range of industries and applications
- Future-ready, designed to incorporate emerging technologies
Cons of SCADA
- Legacy systems lack scalability and have limited support options
- Increased cybersecurity concerns due to interconnected systems
What Is Open Platform Communications (OPC) and Who’s It For?
Open Platform Communications (OPC) is a standard for industrial telecommunications created by an industrial automation task force in 1996. Its primary objective is to enable real-time data communication between control devices from different manufacturers. OPC has evolved significantly over the years and is now utilized in diverse fields including building automation, discrete manufacturing, and process control.
OPC is for industries and individuals who seek a universal standard for data communication between devices. The ability to link different devices in real-time makes it a definitive choice for fields requiring secure and reliable data transfers, for example, the industrial automation sector.
Pros of OPC
- Facilitates real-time data exchange between disparate control devices
- Supports a wide range of platforms, enhancing compatibility
- Audits and enforces end-to-end encryption, boosting system security
Cons of OPC
- Some OPC specifications are limited to OPC Foundation members only
- Requires specific training for system integrators due to its complexity
Deciding the Victor: SCADA vs OPC
SCADA and OPC, both behemoths of the industrial control landscape, have unique selling points. But who should use what? Let’s discern.
Industrial Plant Operators
In the control of complex industrial processes, SCADA is the clear winner. It measures trends over time, detects and corrects issues, offering crucial oversight. Plus, the Human-Machine Interface ensures smooth data processing and operator communication.Invest into SCADA for robust, centralized control.
Telecommunication Entities
In an interconnected world where real-time data comparison between different manufacturers is vital, OPC shines brightly. Built on a foundation of Microsoft’s OLE, COM, DCOM and .NET Framework, it embraces adaptability. Its OPC UA protocol provides essential security and data exchange enhancement. Go for OPC if interoperability and security rank high on your agenda.
Future-facing organizations
SCADA impresses those seeking future-ready solutions. Its roadmap to integrate 5G networks, quantum computing, edge computing, AI and ML offers a promising trajectory. Yet, OPC isn’t far behind in integrating cutting-edge technologies. Specifically, its OPC UA protocol supports operations from microcontrollers to cloud platforms. Both hold promise but SCADA is more visionary.
In this comparison of SCADA vs OPC, SCADA triumphs for industrial operators requiring comprehensive control, while OPC serves telecom entities and those prioritizing security and interoperability. Both are future-oriented, yet SCADA takes a slight edge with its progressive tech integration.
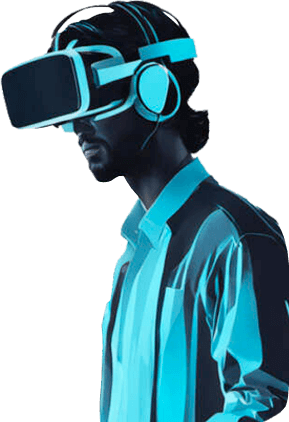